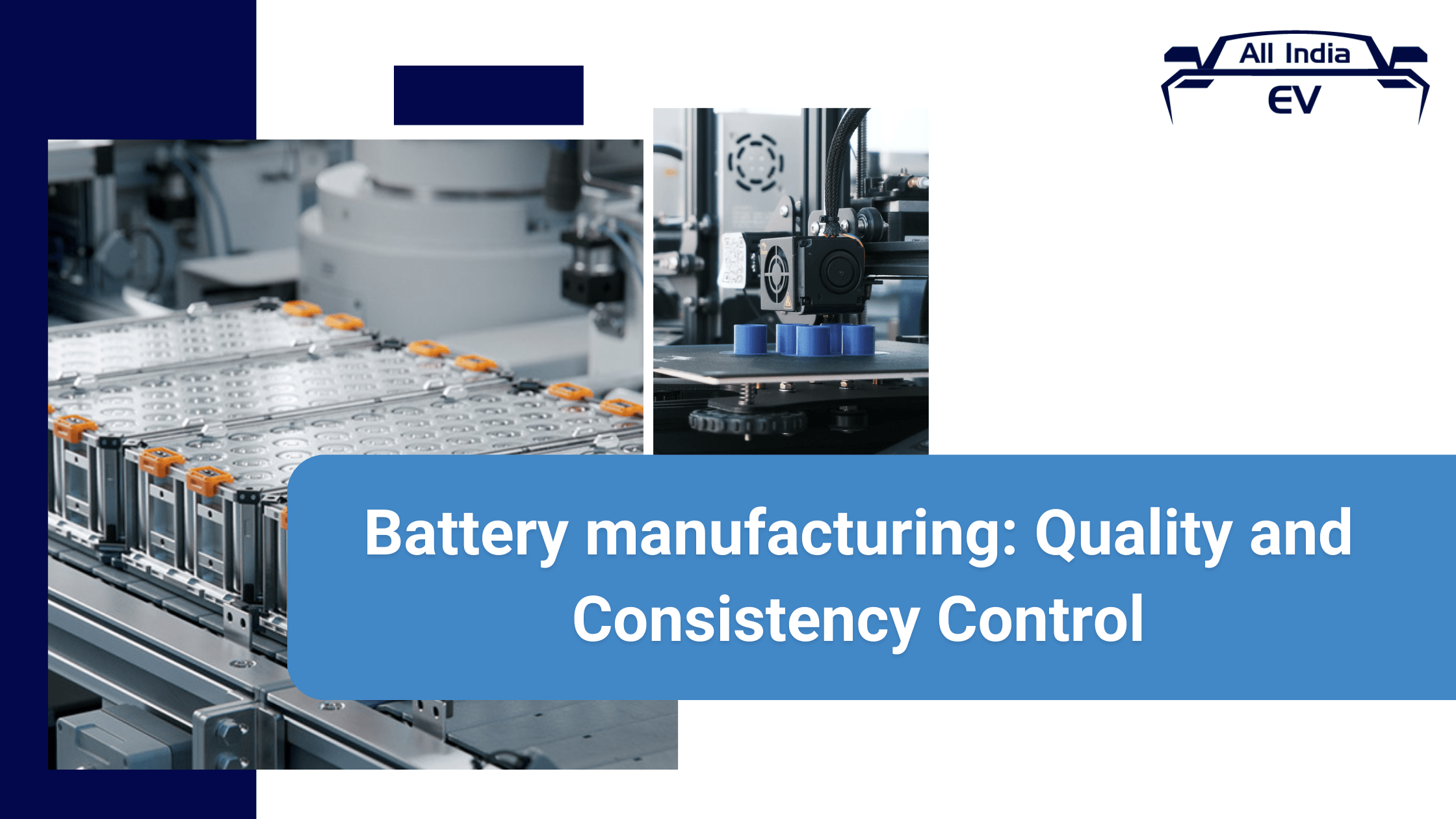
Battery manufacturing: How battery manufacturers ensure the quality and consistency of battery?
In the rapidly evolving world of electric vehicles (EVs), batteries stand as the cornerstone. As the heart of any EV, the quality and consistency of batteries directly influence the vehicle’s performance, safety, and reliability. But how do manufacturers ensure that every battery that rolls off the production line meets the highest standards? Let’s delve into the meticulous world of quality control in battery manufacturing.
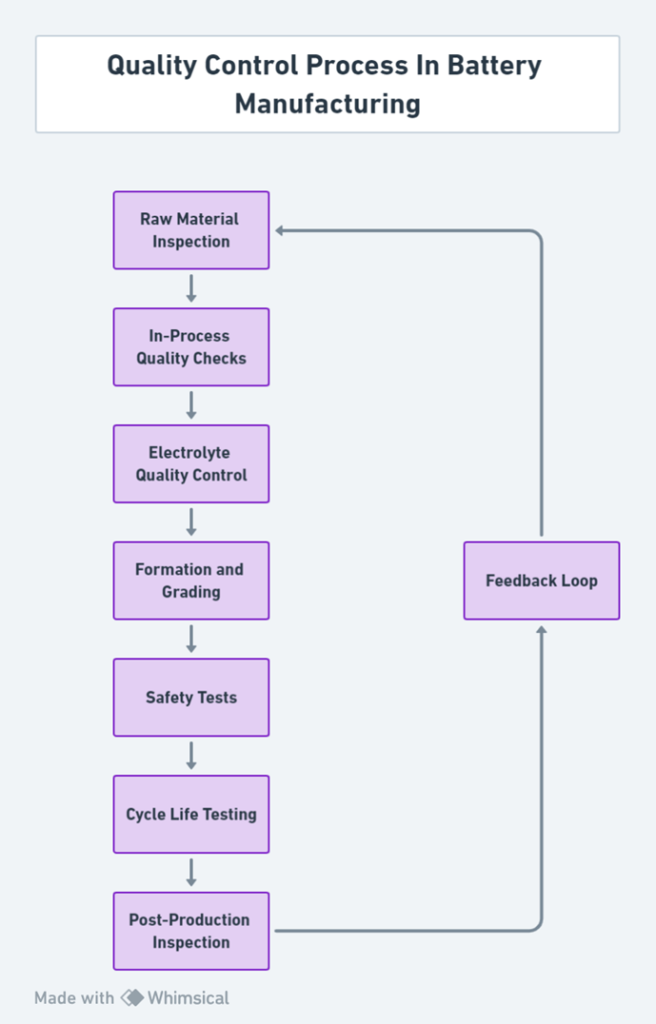
1. Raw Material Inspection: The First Line of Defense
Every battery starts its journey from raw materials like lithium, cobalt, and nickel. Ensuring their purity and consistency is the first step.
How it ensures quality:
⏺️ Supplier Vetting: Manufacturers collaborate with trusted suppliers who adhere to quality standards.
⏺️ Batch Testing: Every batch of raw material undergoes rigorous testing. Impurities, even in minute quantities, can affect battery performance.
⏺️ Storage: Proper storage conditions are maintained to prevent contamination.
2. In-Process Quality Checks: Vigilance at Every Step
As the battery components move through the production stages, continuous checks are essential.
How it ensures quality:
⏺️ Sensor Monitoring: Advanced sensors detect even the slightest deviations, ensuring each battery component meets the desired specifications.
⏺️ Human Oversight: Trained technicians oversee the process, using their expertise to spot and rectify inconsistencies.
⏺️ Equipment Calibration: Regular calibration ensures machines work optimally and provide accurate readings.
3. Electrolyte Quality Control: Ensuring the Right Mix
The electrolyte is the medium that allows ions to flow inside the battery, a critical component for battery function.
How it ensures quality:
⏺️ Composition Testing: Regular tests ensure the electrolyte has the right concentration of components.
⏺️ Contamination Check: Any contaminants can degrade battery performance, so regular checks are vital.
⏺️ Storage: Electrolytes are stored under specific conditions to maintain their purity.
4. Formation and Grading: Shaping and Sorting
Post-assembly, batteries are charged and discharged to shape the internal electrodes and sort them based on performance.
How it ensures quality:
⏺️ Performance Monitoring: Each battery’s voltage, capacity, and internal resistance are tracked.
⏺️ Grading: Batteries are sorted based on their performance, ensuring that only the best make it to the final stages.
5. Safety First: Rigorous Safety Tests
Batteries undergo stringent tests to ensure they’re safe under various conditions.
How it ensures quality:
⏺️ Stress Tests: Batteries are subjected to conditions like overcharging, extreme temperatures, and physical stress to ensure they don’t fail.
⏺️ Failure Analysis: If a battery fails a test, it’s analyzed to understand the cause, helping in continuous improvement.
6. Cycle Life Testing: Simulating Real-World Usage
To gauge a battery’s longevity, it’s subjected to multiple charge-discharge cycles.
How it ensures quality:
⏺️ Longevity Estimation: By cycling the battery until it reaches 80% of its initial capacity, manufacturers can estimate its lifespan.
⏺️ Performance Tracking: The battery’s performance over these cycles gives insights into how it might degrade over time.
7. The Final Check: Post-Production Inspection
Before a battery is shipped, it undergoes one final round of checks.
How it ensures quality:
⏺️ Visual Checks: Technicians look for physical defects or imperfections.
⏺️ Electrical Tests: These ensure the battery’s real-world performance aligns with its specifications.
8. The Feedback Loop: Learning and Improving
Manufacturers maintain open channels of communication with suppliers, customers, and service teams.
How it ensures quality:
⏺️ Issue Identification: Feedback helps pinpoint recurring problems.
⏺️ Continuous Improvement: Based on feedback, changes are made in the production process, leading to better batteries over time.
Conclusion
Quality control in battery manufacturing is a multi-faceted process, combining state-of-the-art technology with rigorous testing protocols. As the demand for EVs continues to grow, ensuring the quality and consistency of batteries becomes even more critical. Through stringent quality control methods, manufacturers are not only ensuring the safety and performance of EVs but also winning the trust of consumers worldwide.
Stay tuned to All India EV for more insights into the intricate world of battery technologies and the EV industry.
Explore the Engineering Marvel of EV Industry with EV Engineering at All India EV