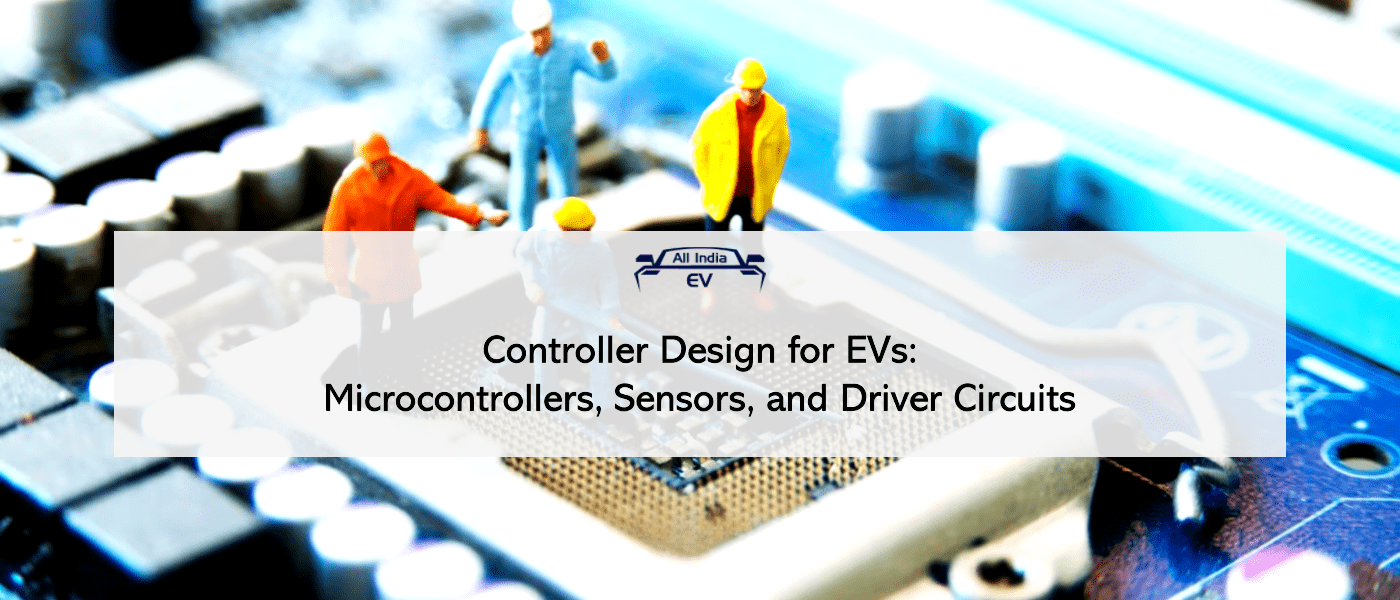
Controller Design for EVs: Microcontrollers, Sensors, and Driver Circuits
Click Here for Introduction to Motor Controller
Electric vehicles (EVs) require efficient and reliable motor control systems to power their traction inverters and drive their electric motors. These systems consist of three main components: microcontrollers (MCUs), sensors, and driver circuits.
Microcontrollers and their role in motor control
Microcontrollers are the components that implement the control logic and algorithm of the motor controller. Microcontrollers are small computers that have a processor, memory, input/output ports, and peripherals, such as timers, analog-to-digital converters (ADCs), and communication interfaces.
Microcontrollers are responsible for:
Reading the inputs from the user interface, such as the accelerator pedal, the brake pedal, or the gear selector, and translating them into the desired speed and torque commands for the motor.
Reading the feedback signals from the sensors, such as the position, speed, current, and temperature sensors, and using them to monitor and regulate the actual speed and torque of the motor.
Generating the control signals for the power electronics, such as the PWM signals for the inverters, and sending them to the driver circuits.
Communicating with other systems in the vehicle, such as the battery management system (BMS), the vehicle control unit (VCU), or the human-machine interface (HMI), and exchanging data and commands.
Sensors: Position, speed, current, and temperature sensors
Sensors are the components that measure the physical parameters of the motor and the power electronics, such as the position, speed, current, and temperature. Sensors provide the feedback signals for the microcontroller, which are used to control and protect the system. Sensors are essential for the motor controller, as they enable the accurate and reliable operation of the motor.
The main sensors in the motor controller are:
Position sensors: Position sensors are the components that measure the angular position of the motor shaft, or the rotor. Position sensors are used to determine the phase and amplitude of the AC voltage for the motor, and to implement the commutation and control methods, such as trapezoidal control, sinusoidal control, or field-oriented control. Position sensors can be classified into absolute or incremental sensors and electrical or mechanical sensors. Examples of position sensors are Hall-effect sensors, optical encoders, or resolvers.
Speed sensors: Speed sensors are the components that measure the angular velocity of the motor shaft, or the rotor. Speed sensors are used to determine the frequency of the AC voltage for the motor, and to implement the speed and torque control methods, such as scalar control, vector control, or direct torque control. Speed sensors can be derived from the position sensors, or separate sensors, such as tachometers or back EMF sensors.
Current sensors: Current sensors are the components that measure the electric current flowing in the motor and the power electronics. Current sensors are used to determine the torque and power of the motor and to implement the current and torque control methods, such as vector control, direct torque control, or maximum torque per ampere (MTPA) control. Current sensors are also used to protect the system from overcurrent, short circuit, or ground fault. Current sensors can be classified into shunt or series sensors, and resistive or magnetic sensors. Examples of current sensors are shunt resistors, current transformers, or Hall-effect sensors.
Temperature sensors: Temperature sensors are the components that measure the temperature of the motor and the power electronics. Temperature sensors are used to monitor and regulate the thermal state of the system and to protect the system from overtemperature, overheating, or thermal runaway. Temperature sensors can be classified into contact or non-contact sensors, and resistive or thermoelectric sensors. Examples of temperature sensors are thermistors, thermocouples, or infrared sensors.
Driver circuits
Driver circuits are the components that amplify and isolate the control signals from the microcontroller to the power electronics. Driver circuits are necessary for the motor controller, as they enable the proper switching and protection of the power devices, such as the MOSFETs or the IGBTs.
The main functions of the driver circuits are:
Amplification: Driver circuits amplify the low-voltage and low-current control signals from the microcontroller to the high-voltage and high-current levels required by the power devices. Driver circuits use transistors or integrated circuits to boost the control signals.
Isolation: Driver circuits isolate the control signals from the power signals, and prevent the noise and interference from the power electronics from affecting the microcontroller. Driver circuits use optocouplers or transformers to isolate the control signals.
Protection: Driver circuits protect the power devices from faults, such as overvoltage, overcurrent, or short circuits, and prevent damage to the power electronics and the motor. Driver circuits use diodes, resistors, or capacitors to protect the power devices.