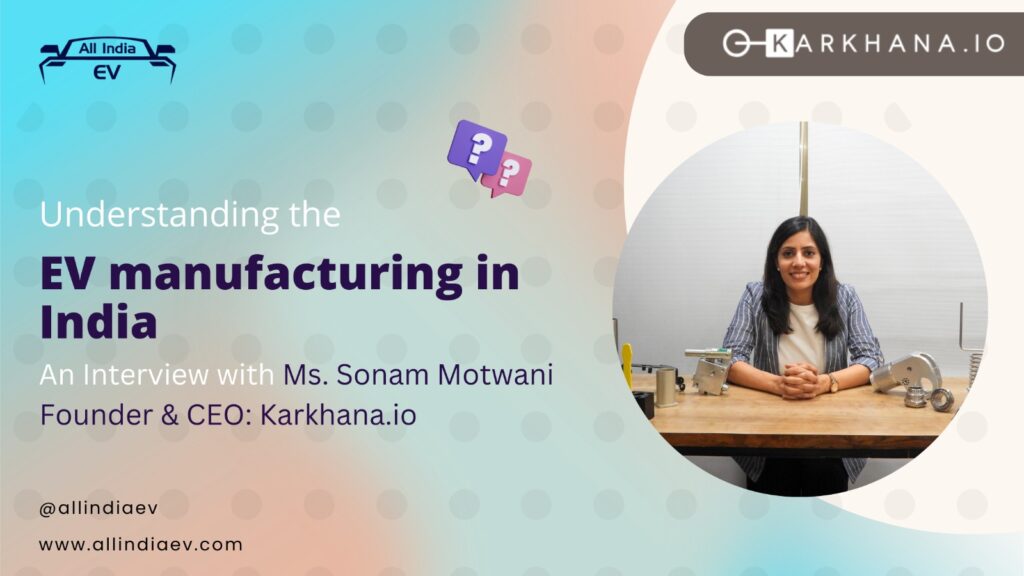
Understand EV Manufacturing in India, an interview with Ms. Sonam Motwani from Karkhana.io
An in-depth discussion with Ms. Sonam Motwani in context to the Manufacturing Side of EV industry…
All India EV: Given your extensive experience in engineering and manufacturing, how do you see innovation playing a role in the evolving landscape of EV manufacturing, especially in terms of improving efficiency and sustainability?
Karkhana.io: In the evolving landscape of EV manufacturing, innovation stands as a pivotal force driving efficiency and sustainability forward. With my extensive experience in engineering and manufacturing, I recognise the profound impact that innovation in:
● Advancements in Battery Technology: Breakthroughs in battery technology, particularly in energy density and charging speeds, are pivotal for enhancing the performance and range of electric vehicles. These innovations enable EVs to travel longer distances on a single charge while reducing charging times, thereby enhancing user convenience and experience. Karkhana.io plays a pivotal role by bridging OEMs with specialised battery technology suppliers, fostering collaboration for the development of more efficient and sustainable energy storage solutions.
● Materials and Lightweighting: The utilisation of lightweight materials is crucial for enhancing energy efficiency and extending the range of EVs. Innovations in materials science, including advanced composites and high-strength alloys, enable the reduction of vehicle weight without compromising safety standards. This contributes to overall performance improvement while minimising environmental impact.
● Charging Infrastructure Innovations: The evolution of charging infrastructure is essential for facilitating widespread EV adoption. Rapid charging technologies, integration with smart grids, and advancements in wireless charging enhance convenience and consumer acceptance. These innovations address concerns related to charging times and accessibility, making EVs a more practical and viable choice for everyday transportation needs.
● Innovative Supply Chain Platforms: The optimisation of the supply chain through digital platforms like Karkhana.io enhances efficiency in EV manufacturing processes. By linking OEMs with a diverse network of certified suppliers, the platform facilitates quicker and more efficient component sourcing while ensuring consistent quality standards. This streamlining reduces lead times and costs, thereby supporting the overall efficiency and sustainability of EV manufacturing endeavours.
✅ Battery Technology Advancements:
Energy Density: Innovations in battery technology, such as improvements in energy density and charging speeds, can significantly enhance the performance and range of electric vehicles.
Karkhana.io can contribute by connecting OEMs with suppliers who specialize in advanced battery technologies, fostering collaboration for the development of more efficient and sustainable energy storage solutions.
✅ Materials and Lightweighting:
The use of lightweight materials in EV manufacturing is essential for improving energy efficiency and extending the range of electric vehicles. Innovations in materials science, such as advanced composites and high-strength alloys, contribute to reducing the overall weight of EVs without compromising safety.
✅ Charging Infrastructure:
Innovations in charging infrastructure are critical for the widespread adoption of EVs. Faster charging technologies, smart grid integration, and advancements in wireless charging can improve the overall convenience and acceptance of electric vehicles.
✅ Innovative Supply Chain Platform for optimization
Streamlining the supply chain through digital platforms like Karkhana.io can play a crucial role in improving efficiency. By connecting OEMs with a diverse network of certified suppliers, the platform facilitates faster and more efficient sourcing of components with consistent high-quality, reducing lead times and costs. This, in turn, supports the overall efficiency of EV manufacturing.
All India EV: From your perspective as the founder of a leading manufacturing supply chain company, what are the most significant challenges in establishing a robust and efficient supply chain for EV manufacturing in India?
Karkhana.io: Establishing a robust and efficient supply chain for EV manufacturing in India presents several significant challenges. One major obstacle is capacity constraints within the supply chain. To address this, we advocate for a collaborative capacity planning approach. By working closely with suppliers, understanding their production capabilities, and maintaining transparent communication channels, we can monitor capacity utilisation in real time. This allows us to make proactive adjustments, ensuring that the production demands for EV components are met.
Another challenge is the fragmented nature of the supply chain. Our solution involves integration and standardisation, encouraging suppliers to adopt standardised processes and technologies through platforms like Karkhana.io. This integration enhances visibility, reduces errors, and fosters a more cohesive and streamlined supply chain.
Consistent quality issues pose a significant hurdle, which we tackle through the implementation of robust quality management systems and supplier training. Our team at Karkhana.io provides training to suppliers, optimising their processes to ensure consistent quality, implement quality assurance plans, and address production-related issues.
Lastly, addressing low turnaround time requires agile supply chain practices. Digital platforms like Karkhana.io offer a one-stop solution, providing a single dashboard for electric vehicle OEMs to work seamlessly with suppliers, quote requirements, and track production processes. This ensures complete visibility, optimisation, and the ability to meet market demands with consistent quality, eliminating the complexities of engaging with multiple stakeholders in the supply chain.
✅ Capacity Constraints:
Solution: Collaborative Capacity Planning
Establishing a collaborative approach to capacity planning is essential. This involves working closely with suppliers to understand their production capabilities and potential constraints. Creating transparent communication channels and leveraging digital platforms can help in real-time monitoring of capacity utilization, enabling proactive adjustments to meet the growing demand for EV components.
✅ Fragmented Supply Chain:
Solution: Integration and Standardization
Integrating the fragmented elements of the supply chain is essential for efficiency. Encouraging suppliers to adopt standardized processes and technologies, possibly through the digital platform offered by Karkhana.io, can streamline the flow of materials and information. This integration enhances visibility, reduces errors, and promotes a more cohesive supply chain.
✅ Consistent Quality Issues:
Solution: Quality Management Systems and Supplier Training
Implementing robust quality management systems is crucial to address consistent quality issues. This involves setting quality standards, conducting regular audits, and providing training to suppliers on quality control measures. Karkhana.io deploys our manufacturing team to train suppliers with the necessary optimization required to ensure consistent quality and implement a quality assurance plan to help them solve issues and errors about production requirements.
✅ Low Turnaround Time:
Solution: Agile Supply Chain Practices
A one-stop solution to streamline the supply chain is crucial to ensure complete visibility and optimization of the production process. Digital platforms like Karkhana.io can help electric vehicle OEMs with a single dashboard to work with suppliers from a pool of vetted networks, quote their requirements and track their production process. This enables them to leverage flexible and scalable solutions and meet market demands with consistent quality and without any hassle of engaging with multiple stakeholders in the supply chain.
All India EV: Considering your success in implementing proprietary tech stacks at Karkhana.io, how do you think advanced technologies can be leveraged to optimize the EV manufacturing process, particularly in areas like sourcing and quality control?
Karkhana.io: At Karkhana.io, our success in implementing proprietary tech stacks underscores the transformative potential of advanced technologies in EV manufacturing. Streamlining the supply chain is paramount, and leveraging digital platforms is key. A one-stop solution, such as Karkhana.io, provides electric vehicle OEMs with a singular dashboard to collaborate with vetted suppliers, streamline sourcing, and enhance quality control.
This approach ensures complete visibility, facilitates efficient production tracking, and empowers manufacturers to meet market demands seamlessly. By embracing flexible and scalable solutions, EV manufacturers can optimise their processes, maintain consistent quality, and eliminate the complexities associated with engaging multiple stakeholders in the supply chain.
A one-stop solution to streamline the supply chain is crucial to ensure complete visibility and optimization of the production process. Digital platforms like Karkhana.io can help electric vehicle OEMs with a single dashboard to work with suppliers from a pool of vetted network, quote their requirements and track their production process. This enables them to leverage flexible and scalable solutions and meet the market demands with consistent quality, complete project tracking and without any hassle of engaging with multiple stakeholders in the supply chain.
All India EV: Based on your experience with capacity expansion projects and your expertise in scalable manufacturing solutions, what strategies would you recommend for EV manufacturers looking to scale their production efficiently?
Karkhana.io: The following strategies for Electric Vehicle (EV) manufacturers aiming to efficiently scale their production:
✅ Boosting Supplier’s Production Capacity:
● Collaborative Capacity Planning: It’s crucial to work closely with suppliers to understand their production constraints and jointly develop plans for capacity expansion. This collaborative approach ensures that the entire supply chain is aligned with the production scaling objectives.
● Diversification of Suppliers: Identifying and engaging with multiple suppliers for critical components can help reduce dependency on a single source. This not only mitigates risks but also provides flexibility in scaling production based on the capabilities of different suppliers.
✅ Streamlining Production Process:
● Process Mapping and Optimisation: Developing detailed process maps for each stage of production and identifying areas for optimisation is key. Implementing Lean Manufacturing principles to eliminate waste and streamline workflows helps reduce production cycle times.
● Tracking Sheet Implementation: Introducing a comprehensive tracking sheet that monitors key metrics at each stage of the manufacturing process allows for real-time visibility into production progress. This enables quick identification and resolution of bottlenecks.
✅ Collaboration with Suppliers to Eliminate Bottlenecks:
● Regular Communication Channels: Establishing regular communication channels with suppliers to address challenges promptly is essential. Conducting periodic meetings to discuss production progress, identify bottlenecks, and collaboratively devise solutions helps keep the process efficient.
● Investment in Supplier Development: Providing support to suppliers by implementing standard operating procedures to standardise production processes can significantly improve efficiency and quality.
✅ Quality Assurance Plan:
● Risk Mitigation through Quality Control: Implementing robust quality control measures at various stages of production to detect and rectify defects early in the process is crucial. This minimises the likelihood of rework and reduces the overall cost of quality.
By implementing these strategies, EV manufacturers can navigate the complexities of scaling production efficiently while maintaining a resilient and agile supply chain.
✅ Boosting Supplier’s Production Capacity:
Collaborative Capacity Planning: Work closely with suppliers to understand their production constraints and jointly develop plans for capacity expansion. This collaborative approach ensures that the entire supply chain is aligned with the production scaling objectives.
- ✅ Diversification of Suppliers:
Identify and engage with multiple suppliers for critical components to reduce dependency on a single source. This not only mitigates risks but also provides flexibility in scaling production based on the capabilities of different suppliers.
✅ Streamlining Production Process:
Process Mapping and Optimization: Develop detailed process maps for each stage of production and identify areas for optimization. Implement Lean Manufacturing principles to eliminate waste and streamline workflows, reducing production cycle times.
Tracking Sheet Implementation: Introduce a comprehensive tracking sheet that monitors key metrics at each stage of the manufacturing process. This allows real-time visibility into production progress, enabling quick identification and resolution of bottlenecks.
✅ Collaboration with Suppliers to Eliminate Bottlenecks:
Regular Communication Channels: Establish regular communication channels with suppliers to address challenges promptly. Conduct periodic meetings to discuss production progress, identify bottlenecks, and collaboratively devise solutions.
Investment in Supplier Development: Provide support to suppliers by implementing standard operating procedures to standardize production processes.
✅ Quality Assurance Plan:
Risk Mitigation through Quality Control: Implement robust quality control measures at various stages of production to detect and rectify defects early in the process. This minimizes the likelihood of rework and reduces the overall cost of quality.
All India EV: As an industry leader with a deep understanding of manufacturing trends, what future developments do you foresee in the EV manufacturing sector, and how should companies prepare to adapt to these changes?
Karkhana.io: As the EV manufacturing industry moves forward, several pivotal developments will be shaping its future. Firstly, advancements in battery technology will continue, leading to higher energy density, faster charging times, and reduced costs. To adapt, companies must prioritise R&D investments, forge partnerships with battery manufacturers, and secure robust supply chains.
Secondly, consumers will increasingly demand EVs with extended ranges, superior performance, and rapid acceleration. To meet these expectations, companies should focus on enhancing engineering capabilities, leveraging lightweight materials, optimising aerodynamics, and refining powertrains.
Furthermore, the expansion of charging infrastructure will be critical to assuage range anxiety and bolster widespread EV adoption. Companies ought to collaborate with governments and stakeholders, investing in innovative charging solutions and fast-charging technologies.
Moreover, as EV adoption surges globally, companies must diversify markets and expand their global footprint. This entails developing adaptable models tailored to diverse markets, forging local partnerships for product localization, and investing in a resilient global supply chain.
Lastly, amidst evolving dynamics, building resilient and diversified supply chains remains paramount. Strengthening relationships with key suppliers, diversifying sourcing, and implementing contingency plans will fortify companies against potential disruptions.
In essence, embracing these future trends and adaptation strategies will position companies at the forefront of the burgeoning EV manufacturing sector.
✅ Advancements in Battery Technology:
Future Trend: Continued advancements in battery technology, including higher energy density, faster charging times, and lower costs.
Adaptation Strategy: Companies should invest in research and development to stay at the forefront of battery innovations. Establish partnerships with battery manufacturers and suppliers to ensure a stable supply chain.
✅ Increased Range and Performance:
Future Trend: Consumers are likely to demand EVs with longer ranges, improved performance, and faster acceleration.
Adaptation Strategy: Focus on engineering capabilities to enhance the range and performance of electric vehicles. Invest in lightweight materials, aerodynamics, and efficient powertrains.
✅ Charging Infrastructure Expansion:
Future Trend: Growth in charging infrastructure to address range anxiety and facilitate widespread EV adoption.
Adaptation Strategy: Collaborate with governments and other stakeholders to invest in charging infrastructure. Companies can also develop innovative solutions like fast-charging technologies.
✅ Market Diversification and Global Expansion:
Future Trend: Companies expanding their market presence globally as EV adoption increases worldwide.
Adaptation Strategy: Develop models suitable for diverse markets, considering regional preferences and regulations. Establish partnerships with local companies for product localization and invest in a global supply chain.
✅ Supply Chain Resilience:
Future Trend: Ongoing focus on building resilient and diversified supply chains to mitigate risks.
Adaptation Strategy: Strengthen relationships with key suppliers, diversify sourcing, and invest in contingency planning to address potential disruptions in the supply chain.