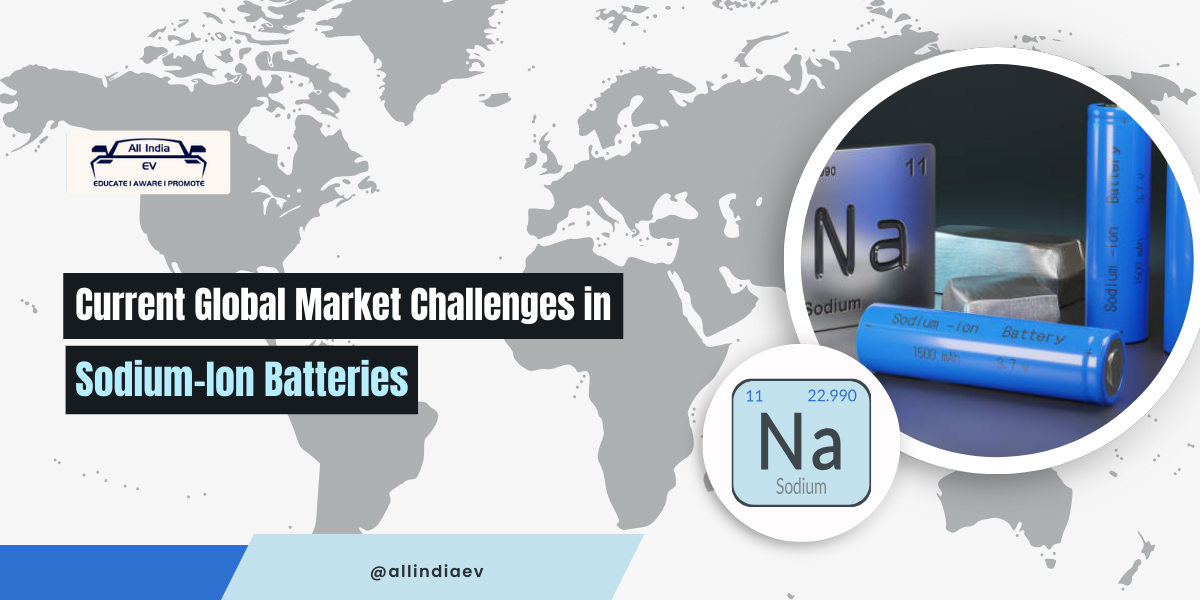
Electric vehicle battery of the future: Govt & private sector must focus on Na-ion technology
Electronics industry uses Na-ion batteries in abundance while grid power storage uses this on account of cost benefit and safety. Research is going on in various laboratories all over the world to pack more energy per unit weight. The following article is credited to Dr. Arunaditya Sahay. Internal combustion engine powered vehicles have a fuel tank in which chemical energy is packed in the form of petrol/diesel/CNG/PNG. Likewise, electric vehicles have a battery pack assembly in which energy producing cells are packed.
The batteries used in ICE powered vehicles are for the purpose of starting the engine whereas the battery of an EV is meant to provide power to the vehicle for its mobility. Two battery technologies – sodium- ion and lithium-ion – have been most promising for various applications, each having unique strengths and weaknesses, making it suitable for different applications.
Sodium-ion battery was developed in the 1970s and early 1980s whereas lithium-ion battery was developed by the 1990s which demonstrated higher energy density, thus, showed higher commercial promise. High energy Li-ion storage batteries were first developed and commercialized by Sony Corporation of Japan in 1991 revolutionizing the energy storage industry.
Li-ion batteries have since then become the dominant technology in electric vehicles (EVs), portable electronics, and grid storage applications. The Li-ion battery, first developed for electronics application, was later developed into a large energy storage EV battery that could deliver energy levels similar to fossil fuel used in traditional ICE vehicles.
Though the Li-ion battery was first developed in Japan, it was China that made great strides in large Li-ion batteries needed in automobiles. Today, 60% of the global demand for batteries is met by Chinese Li-ion battery manufacturers. Korea at 22% and Japan at around 8% hold the 2nd and 3rd position in EV battery manufacturing and supply. Tata Motors, Mahindra & Mahindra, Reliance, Amara Raja and Excide have announced their plan for EV battery manufacturing.
India needs to develop a reliable upstream supply chain. Luckily, lithium has been discovered in Reasi (J&K) and Katghora (Chhattisgarh). To help the battery manufacturers, the government of India has come out with an advanced cell chemistry (ACC) production linked incentive (PLI) scheme to support 50 GWH battery manufacturing providing an outlay of INR 18,100 crore.
The battery pack is the main cost (30-40%) in EV followed by the main body (20-30%), electric motor (15-20%), power electronics (10-15%), interior and infotainment (10-15%) and thermal management system (5- 10%). The Li-ion battery used in EVs basically consists of a cathode (typically made of lithium iron phosphate, lithium cobalt oxide, or other lithium compounds), an anode (usually graphite), and an electrolyte that facilitates the movement of lithium ions between the two electrodes while charging and discharging of the battery.
The cathode, which generally consists of metals like lithium, nickel, cobalt, and manganese is the most expensive part of the battery. Anode is usually made from graphite or silicon-based materials while most commonly used electrolyte consists of lithium salt, such as LiPF6 in an organic solution. Further, there is a membrane made of Polyolefin or Ceramic-Coated material to separate the anode and the cathode while allowing ion flow during charging and discharging. In such EV batteries, the cell materials are the major cost (60-70%).
Not only are Li-ion batteries costlier compared to Ni-ion batteries but they are prone to catching fire. Several incidences of fire were observed in EVs all over the world; the fire emanated out of the battery pack. For example, in Incheon, Korea a Mercedes-Benz caught fire in the underground parking lot of an apartment complex. Firefighters struggled for more than eight hours to extinguish the blaze. Investigation showed that the cause of the fire was overheating of the battery.
Back home in India, there have been quite a few cases of fire in cars and scooters. The investigations showed poor quality of battery, overheating of battery and short circuit. Therefore, safety of Li-ion batteries has become a concern for the manufacturers as well as users. In the deployment of battery technologies, especially in applications like electric vehicles, safety of the battery is critical. Li-ion batteries have improved in quality over time and are now generally safe but in case of thermal runaway, they are still prone to fires or explosions under certain conditions. High energy density, on one hand is beneficial for EV but on the other this proves to be a great weakness because of the flammability of the organic electrolytes used in Li-ion batteries.
Na-ion batteries which have lower energy density use safer materials which are less prone to thermal runaway, therefore, this battery technology is an attractive option. Furthermore, it is 30% less costly compared to Li-ion batteries. Both Na and Li belong to group 1 of the periodic table but Li is a rare material while Na is found in abundance.
Electronics industry uses Na-ion batteries in abundance while grid power storage uses this on account of cost benefit and safety. Research is going on in various laboratories all over the world to pack more energy per unit weight. Once it matches the energy density of Li-ion batteries, it will become the preferred choice of all manufacturers and users. Though lithium deposits have been discovered in our country in Reasi and
Katghora, it will take a long time to extract lithium. The refining of lithium is still far away making us dependable on China for downstream battery manufacturing. Of late, Reliance Industries has purchased Faradion, a UK start-up developing sodium ion batteries. They propose to invest a further $35 million in Faradion for accelerating the commercialization of its products, including batteries for electric vehicles. Along with commercialization, they will do well to invest in R&D to bring present energy density of 150 Watt hour/kg to 200 Watt-hr/kg which will open for them the EV market as well.
A serious thought needs to be given to the development of proper Na-ion battery manufacturing technology suiting EV application. Our country has an abundance of sodium being surrounded by sea on three sides.
(The author is former MD of Scooters India Ltd., currently serving as Distinguished Professor; Views are personal)