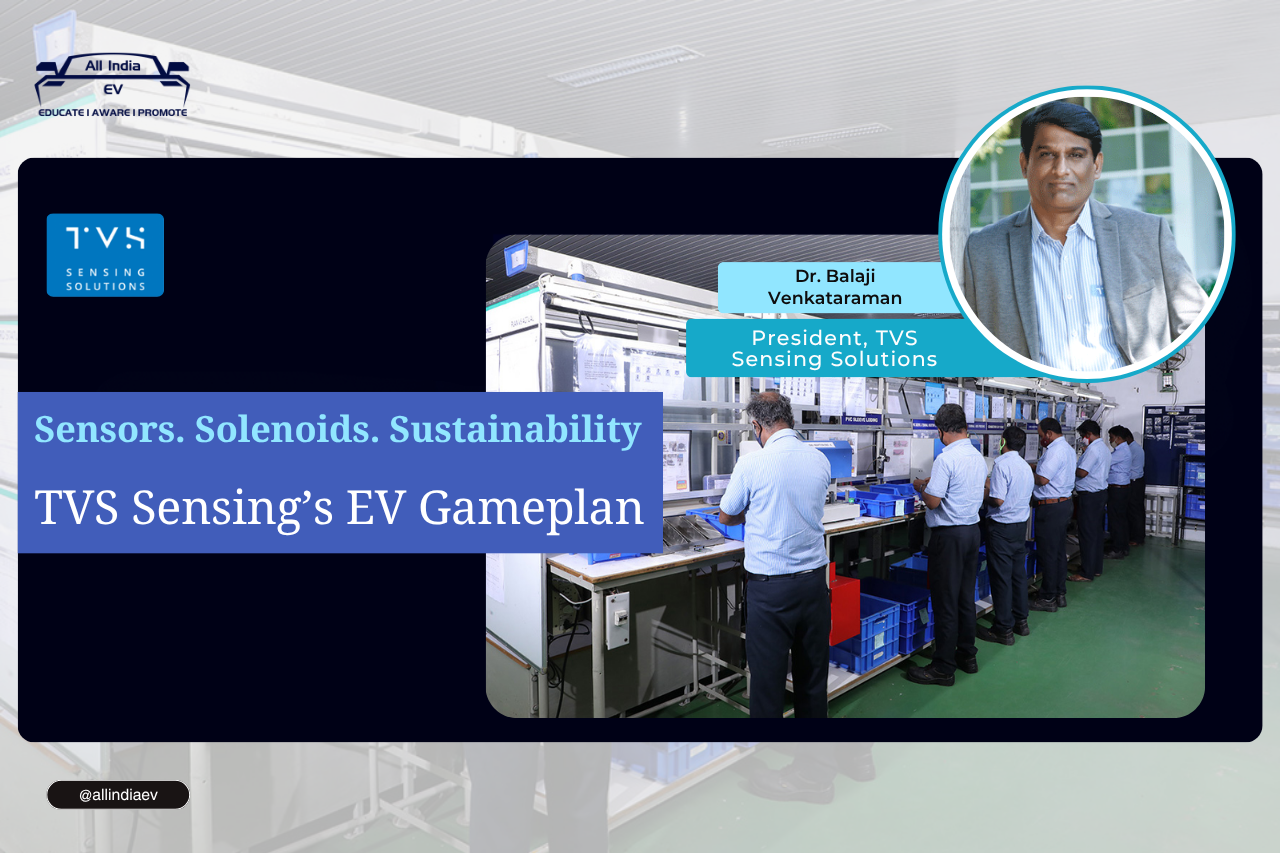
TVS Sensing Solutions Redefining Sensor Technology for Electric Vehicles
India’s electric vehicle (EV) sector is evolving at an unprecedented pace. In the first half of 2025 alone, EV sales crossed 140,000 units, marking a significant year-on-year growth and underscoring the shift towards sustainable mobility. Yet, while the adoption curve is steep, the industry faces unique challenges—ranging from the localization of critical components to thermal management and supply chain constraints for high-performance EV parts.
At All India EV, we’ve been closely tracking these trends. To understand how component innovation is shaping the future of Indian EVs, we engaged with TVS Sensing Solutions, a leading Tier‑1 supplier.
In this exclusive conversation, Dr. Balaji Venkataraman, President of TVS SS, discusses how the company is rethinking sensor and solenoid technologies for EV-grade performance, enabling OEMs to address energy efficiency, durability, and sustainability demands.
Inside TVS Sensing Solutions’ Vision: Redefining Sensor Tech for EVs
What are the key differences in design requirements between sensors or solenoids for ICE vehicles versus electric vehicles?
Sensors and solenoids in ICE vehicles and EVs differ in their design given various features such as power source, voltage levels, movement and customization. ICE vehicles components are built for lower voltage, whereas EVs use high-voltage systems requiring better insulation and safety features. Cooling methods and component layout also vary, with ICE parts often air-cooled and built to fit around bulky engines, while EV components are optimized for thermal efficiency and space within battery-driven architectures.
For example – our speed sensor for E-bikes and the active wheel speed sensor used in ICE vehicles differ in design despite sharing features like customizable cable length and connectors. While the E-bike sensor is a Hall-based device mounted on the hub motor stator, the active wheel speed sensor is used in ICE vehicles is externally mounted near a rotating toothed or magnetic ring to measure wheel rotational speed, enabling systems like ABS.
Can you walk us through any unique materials or manufacturing processes TVS Sensing has adopted to meet EV-grade performance, durability, and thermal requirements?
We have strategically adopted a combination of specialized materials and advanced manufacturing processes created for our EV solutions to meet the demanding performance, durability and thermal requirements of EV-grade components. Our materials including ferrous and non-ferrous metals, engineering plastics, copper (Cu), brass, beryllium copper (BeCu) and silver are chosen for their high conductivity, corrosion resistance and mechanical stability at high temperatures.
These materials enable the best thermal management and long-term performance in high-voltage. For components like sensors and solenoids, we use micro moulding, in-house tooling and EDM/wire cutting technologies to produce intricate parts with tight tolerances and short lead times. Our A & B sample prototyping approach allows rapid iterations in plastic, metal and wiring harnesses which is ideal for EV product development cycles.
How does TVS SS approach customization for different OEMs’ EV platforms? Are there modular design families that streamline development?
We entered the EV sector with a diverse portfolio of products manufactured for this industry. We aim to establish a substantial presence in the Indian EV Market providing advanced solutions that facilitate electrification.
As a Tier 1 supplier, we prioritize understanding and addressing OEMs particular requirements. Customization, quality, dependability and quick delivery are key to their growth. We have formed collaborations with EV startups focused on innovation, continual development and cost reduction.
Additionally, our application engineering team offers deep customization to reduce weight, improve thermal behaviour and extend electrical life which is remains critical for next-generation electric vehicles. We are also actively looking to collaborate with technology companies to develop innovative solutions that improve vehicle performance, quality and create added value for customers.
Which sensors in your EV line most directly impact battery performance and energy efficiency—and how?
Our Motor Hall Sensor PCB is designed to provide accurate speed and phase position feedback for hub-based BLDC motors in two-wheeler electric vehicles. By ensuring accurate control signals to the motor controller, the sensor contributes directly to improved energy efficiency, optimized battery usage and extended vehicle range. The sensor’s compact integration within the motor also helps reduce wiring complexity and system losses in electric two-wheelers.
Our Speed and Direction Sensor is built for industrial and commercial electric drive applications such as traction motors, conveyors and material handling equipment. It provides real-time measurement of both rotational speed and direction enabling precise bidirectional control critical for electric mobility and automation systems.
By improving motion control accuracy and reducing unnecessary energy consumption, this sensor enhances the overall efficiency of the drive system and helps extend battery life and supports consistent performance in demanding environments like commercial vehicles and electric industrial equipment.
What in-house or third-party validation and testing regimes do your EV components undergo to ensure high reliability over the vehicle’s lifetime?
We have established a robust and application-specific Quality Assurance and Reliability Testing regime to ensure consistent performance of our EV components throughout the vehicle’s lifetime. Each component undergoes custom-built End-of-Line (EOL) testing designed to validate 100% functionality before it leaves the production line. These EOL testers are custom-made for critical EV components such as sensors and check for electrical parameters, signal accuracy and response times under simulated operating conditions.
To further ensure product integrity, we use leak testing systems especially for components exposed to harsh environments or requiring IP-rated protection. These testers detect seal failures, ensuring components maintain their protective enclosure against moisture, dust and thermal cycling. This comprehensive testing regime combined with endurance and lifecycle validation ensures that our EV components consistently deliver long-term reliability, safety and optimal performance throughout the entire service life of the vehicle.
Beyond improving vehicle efficiency, how is TVS Sensing minimizing the environmental footprint of its own manufacturing processes for EV components?
We are committed to integrating sustainable principles into every stage of our product development and solutions with a strong focus on resource efficiency and life cycle impact. Our approach goes across the value chain where we prioritize supply chain sustainability and ensure ethical practices and fair labour conditions are followed throughout. We are actively following net-zero impact initiatives through measures such as water conservation, energy-efficient LED lighting and the installation of solar panels.
Our manufacturing process for EV components is designed with a strong focus on precision, efficiency and sustainability ensuring that every part meets the high-performance demands of electric mobility while minimizing environmental impact. We also follow value engineering practices to optimize material usage, reduce waste and lower overall carbon footprint while meeting performance and thermal requirements for EV-grade applications. The entire process is built to support scalable, cost-effective and environmentally responsible manufacturing for the future of electric mobility.
Could you highlight one or two high-impact R&D initiatives underway (e.g., next-gen sensor technologies, smart features)?
Our Development and Innovation Center drives our efforts to stay ahead of industry trends by creating technology-led solutions. One of our key R&D initiatives focuses the manufacturing process in the insert molded space for sophisticated product assemblies.
For example – in the sensor domain, we focus on integrating multiple sensing elements into a single unit to optimize space and deliver cost-effective solutions to our customers.
We are actively working on Integrated Sensors and Advanced Driver Assistance Systems (ADAS), which support important functions like lane-keeping, parking assistance, cruise control and collision avoidance. These technologies improve vehicle safety and performance while moving us closer to autonomous driving and showing our commitment to innovation in the EV space.
What do you see as the biggest technical and market challenges for EV components over the next 3–5 years, and how is TVS SS preparing to address them?
In recent years the demand for electric vehicles has grown rapidly as government regulations on emissions and the global push for cleaner transportation increase. Several key factors such as advancements in battery technology, consumer demand for sustainable mobility and the increasing need for auto components in electric and hybrid vehicles are fuelling this market expansion.
Despite this momentum, there are several challenges both – technical and market. On the technical front, components must deliver high precision, durability and thermal stability in compact, high-voltage environments. Integrating multiple functions into smaller sensor units adds to design complexity.
At the same time, we must address market pressures such as cost competitiveness, supply chain constraint and the need to rapidly scale up production while maintaining quality.
As India aims for 30% electric vehicle penetration by 2030, the focus is steadily moving beyond just vehicle design to the critical components that ensure performance, safety, and longevity. TVS Sensing Solutions stands out as a key player in this transformation—leveraging advanced materials, precision engineering, and integrated technologies to deliver next-generation solutions for EVs.
Their emphasis on homegrown innovation, sustainable manufacturing practices, and deep customization for diverse OEM platforms highlights the role Tier‑1 suppliers will play in building a resilient EV ecosystem in India. As global and domestic players accelerate electrification, companies like TVS SS are ensuring India is not just part of the EV revolution but helping lead it from the ground up.