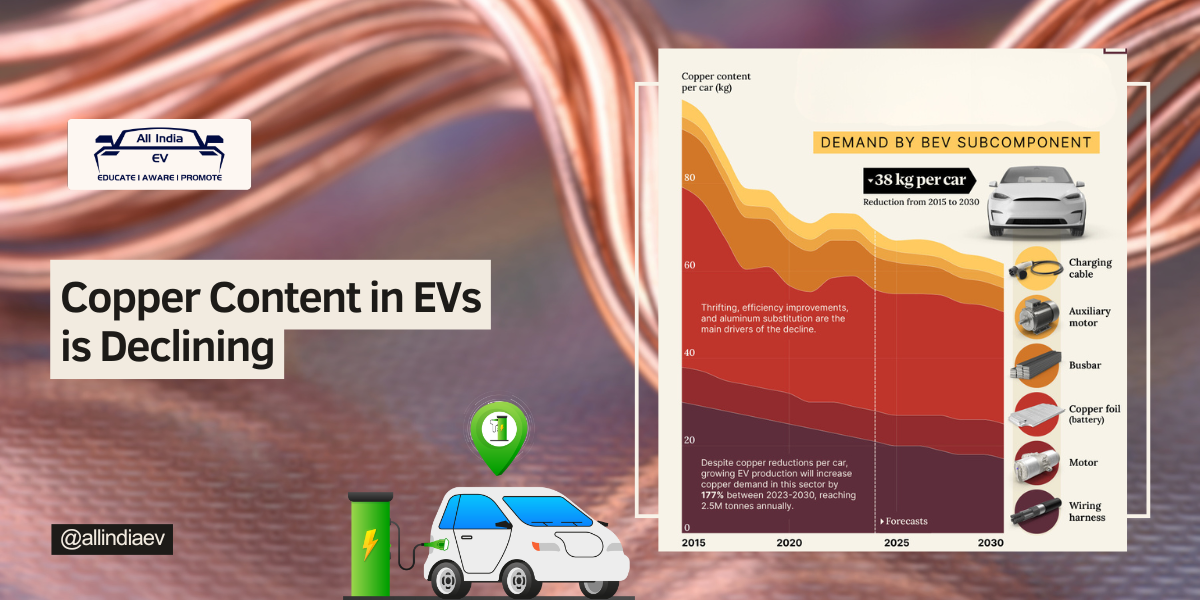
Declining Copper Usage in Electric Vehicles: What’s Happening and What’s Next?
The electric vehicle (EV) industry has seen incredible growth over the last ten years, largely due to advances in technology and a global push to lower carbon emissions. Copper has always been a key material in EV production because of its excellent ability to conduct electricity. It’s used in important parts like wiring, motors, and batteries. But things are changing. Over the last decade, the amount of copper used per vehicle has been steadily decreasing. This is because manufacturers are adopting more efficient technologies and using alternative materials like aluminum
.Let’s dive into why copper usage is going down, how this affects India’s electric vehicle economy, and what the future holds.
Why is Copper Use Declining in EVs?
According to data from Benchmark Mineral Intelligence, the amount of copper used in each electric vehicle (also called “copper intensity”) has been dropping over the years. For example, in 2015, about 99 kilograms (kg) of copper was used in a typical battery electric vehicle (BEV). By 2030, that number is expected to shrink to 62 kg. Several factors are driving this change:
🔻 Thinner Copper Foils in Batteries: Copper foil is a crucial part of the battery anode (a part of the battery where electricity flows out). In 2015, each vehicle used around 41 kg of copper foil. However, with improvements, thinner foils are now being used, and by 2030, only 26 kg will be needed.
🔻 Reduced Copper in Wiring: Advances in wiring technology have allowed manufacturers to reduce the amount of copper used in EVs. In 2015, 30 kg of copper was used for wiring each vehicle, but by 2030, it’s expected to drop to 17 kg.
🔻 More Efficient Motors: EV motors have become smaller and more efficient, meaning they don’t require as much copper. The copper used in other parts, like auxiliary motors and charging cables, is also decreasing as technology improves.
🔻 Switch to Aluminum: In some areas, copper is being replaced by aluminum. Although aluminum requires more space to provide the same electrical conductivity, it’s cheaper and lighter, making it an appealing alternative for certain components like wiring and busbars (a type of electrical junction).
Here’s a breakdown of how copper usage has changed and is projected to change in EVs:
Year | Wiring (kg) | Motor (kg) | Copper Foil (kg) | Busbar (kg) | Auxiliary Motor (kg) | Charging Cable (kg) | Total (kg) |
---|---|---|---|---|---|---|---|
2015 | 30 | 8 | 41.26 | 13.23 | 2.87 | 3.96 | 99.32 |
2020 | 25 | 7 | 24.71 | 10.24 | 2.73 | 3.76 | 73.44 |
2025 | 20 | 7 | 27.79 | 7.19 | 2.52 | 2.51 | 67.01 |
2030 | 17 | 8 | 25.63 | 5.44 | 2.37 | 3.26 | 61.70 |
The Bigger Picture: Copper Demand Still Rising
Here’s the interesting part: even though each individual electric vehicle is using less copper, the overall demand for copper is actually going up. Why? Because the number of electric vehicles being produced is skyrocketing. According to estimates, the copper demand from the EV sector will jump from 56,000 tonnes in 2015 to a whopping 2.5 million tonnes by 2030.
This may seem like a paradox. How can copper usage per vehicle go down while the total demand goes up? It’s all about volume—the rapid growth in EV production means that, even with less copper per car, more cars are being made, which keeps demand high.
Here’s a quick look at the growth of copper demand in EVs:
Year | Copper Demand (tonnes) |
---|---|
2015 | 56K |
2020 | 237K |
2025F | 1.2M |
2030F | 2.5M |
What Does This Mean for India’s Electric Vehicle Market?
India is fast emerging as a key player in the global EV industry. Government programs like the Faster Adoption and Manufacturing of Electric Vehicles (FAME) scheme and Production-Linked Incentives (PLI) are driving investment in this sector. But with the decline in copper usage, there are some important implications for India:
🔹 Lower Manufacturing Costs: Copper is expensive, so using less of it (and substituting with cheaper materials like aluminum) can bring down the cost of making electric vehicles. This is great news for India, where consumers are very price-sensitive. Cheaper production can help make EVs more affordable, boosting both domestic and global competitiveness for Indian manufacturers.
🔹 Reduced Dependence on Copper Imports: India imports a large chunk of the copper it uses. By cutting down on the copper needed for EV production, India could become less reliant on these imports, which would improve supply chain stability and protect the country from fluctuating copper prices.
🔹 Boost for Aluminum Producers: As more manufacturers switch to aluminum in place of copper, India’s aluminum industry could see significant growth. India is one of the largest producers of aluminum, so this shift could create more jobs and opportunities in the sector.
🔹 Environmental Benefits: Mining and extracting copper is an energy-intensive and environmentally damaging process. Reducing copper usage can help lessen the environmental impact of EV production, aligning with India’s broader goals of sustainability.
🔹 Challenges for the Copper Industry: On the flip side, India’s copper industry might face challenges as demand from the EV sector decreases. Copper producers may need to look for new markets or industries to make up for the loss in demand from the automotive sector.
Wrapping Up
The trend of using less copper in each electric vehicle is clear, and it’s going to have a big impact on the future of EV production. For India, this shift brings both opportunities and challenges. On one hand, it can help lower production costs, improve supply chain resilience, and support a more sustainable economy. On the other hand, the copper industry will need to adapt to the declining demand from the EV sector.
Despite the challenges, copper will remain a critical material for the booming EV market globally. The key for India will be to embrace these material changes while continuing to grow its position as a leader in the electric vehicle space.
In India, where the demand for lithium-ion batteries is rapidly increasing, ensuring the safety and reliability of these batteries is of utmost importance. Whether for electric vehicles, consumer electronics, or renewable energy storage, following both international and Indian testing standards is critical. Rigorous testing, including vibration testing, ensures that lithium batteries meet the highest quality standards. By adhering to these protocols, manufacturers can guarantee the safety and performance of their products, thus fostering consumer trust and supporting the continued growth of this technology.